AI-driven Automated Structural Health Monitoring (see full blog here)
Published:
Mechanics-Informed Autoencoder Enables Automated Detection and Localization of Unforeseen Structural Damage
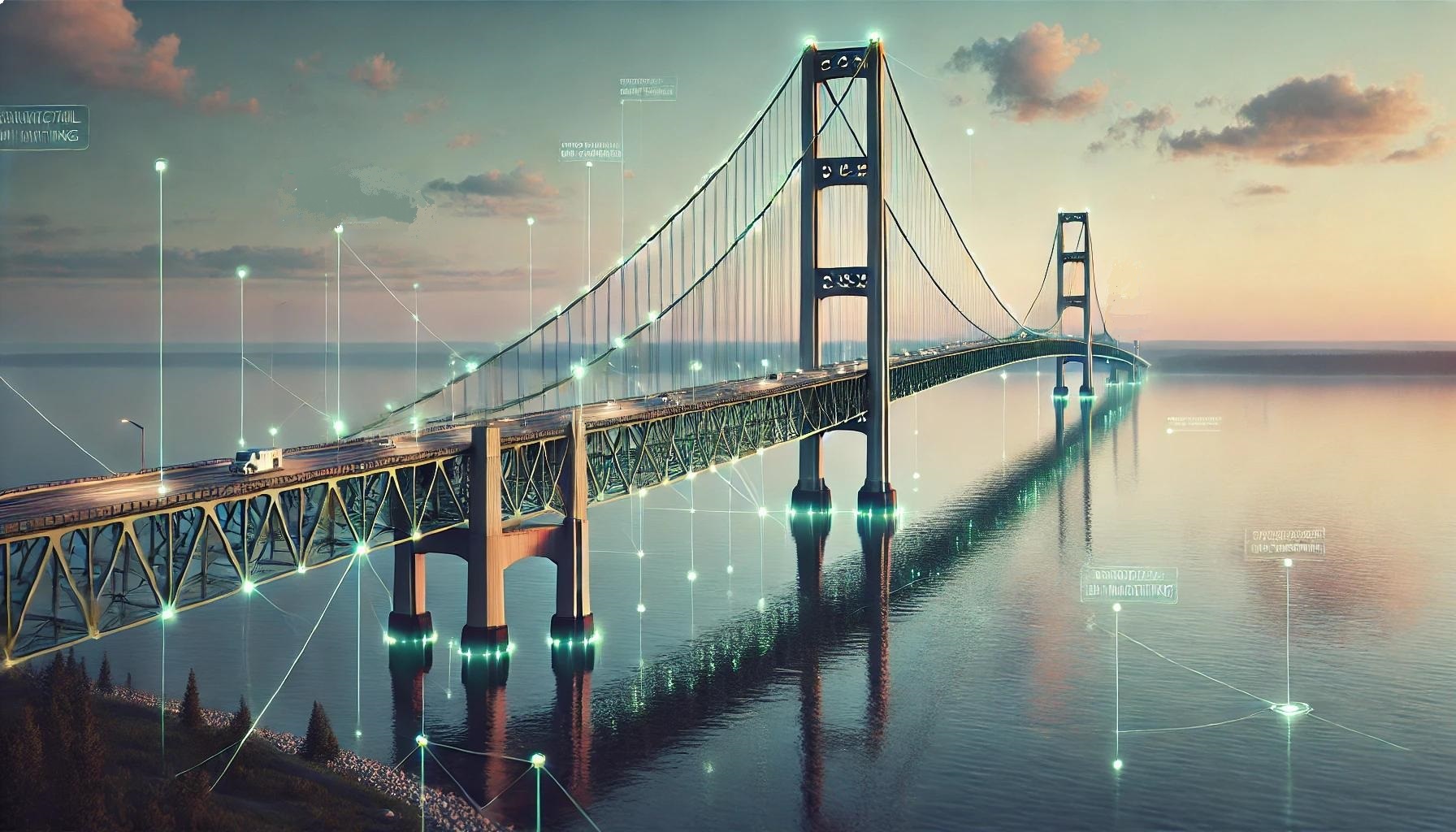
See blog post at Nature Research Communities Infrastructure resilience is emerging as a crucial need in the face of increased risks and hazards impacts. This highlights the need for reliable, cost-effective, and scalable infrastructure condition assessment and monitoring approaches. The need is driven by recent real-world failures that have led to catastrophic consequences, from the unnoticed cracks in the I-40 Bridge in Memphis, which resulted in an emergency closure, to the collapse of a bridge in Pittsburgh in 2022 due to undetected corrosion. These incidents reveal the limitations of traditional inspection methods and emphasize the need for more intelligent and efficient solutions. To prevent future catastrophes, it is essential to develop accurate baseline models that are scalable, generalizable, and tailored to the unique characteristics of each structure. AI-driven automated Structural Health Monitoring (SHM) systems offer a promising avenue to address the shortcomings of existing manual inspections and sensor technologies. By leveraging advanced algorithms and machine learning techniques, these systems can enhance early detection and localization of structural damage, thereby significantly improving infrastructure resilience and safety.
In this research, we introduce a framework named MIDAS, which stands for Mechanics-Informed Damage Assessment of Structures. It is a synergistic integration of entirely passive measurements from inexpensive sensors, data compression, and a mechanics-informed autoencoder. MIDAS detects and localizes damage in real time by creating a bespoke baseline model for each structure.
Story behind MIDAS
The idea for this research was sparked by the increasing interest in SHM, advanced sensor technologies, and sensor data fusion. We aimed to develop a solution that could be applied broadly to existing structures, combining entirely passive sensor technology for automation with AI algorithms for enhanced performance. This generalization required us to avoid relying on specific damage knowledge or case-dependent information. The concept began to take shape in 2022, initially focusing solely on damage detection. We sought to integrate advanced machine learning algorithms with fundamental mechanical principles. Through numerous iterations and refinements, we eventually distilled our approach into the one presented in the paper.
Our journey started with numerical simulations to establish proof of concept. We tested various damage configurations and designed laboratory experiments to validate our methods. Based on feedback from the first round of peer review, we realized the need to enhance the real-world applicability of our study. This led us to conduct additional experiments and simulations, addressing factors such as scalability, environmental variations, and the number and placement of sensors. These revision enabled us to align our research with real-world operational conditions, ultimately translating our work into feasible and practical solutions.
How MIDAS Works
The MIDAS framework advances damage detection and localization by integrating mechanics-based knowledge into neural networks. It starts with compressed sensor data from an undamaged structure, using this data to reconstruct and establish a baseline model.
MIDAS does not require data from damaged structures for training, which is a significant advantage of our method, given that collecting realistic damaged data on large-scale structures is practically infeasible. The loss function is a hybrid of traditional mean squared error and a mechanics-informed term. This term incorporates domain-specific knowledge, minimizing deviations in pairwise mechanical relationships between responses and strengthening sensor correlation.
Our approach enhances the accuracy of the baseline model for undamaged structures and improves sensitivity to subtle damage. Damage detection is achieved by comparing the reconstruction error of the instantaneous sensor data in time windows with that of the undamaged baseline. To localize the damage, we further compute the norms of reconstruction errors at each sensor and interpolate them between the sensors. With the integrated mechanical knowledge, MIDAS significantly improves its performance in detecting and localizing damage early when it is minor. Additionally, incorporating data compression affords robustness to sensor noise and enables more efficient data processing, network training, and prediction, facilitating near-real-time damage detection and localization.
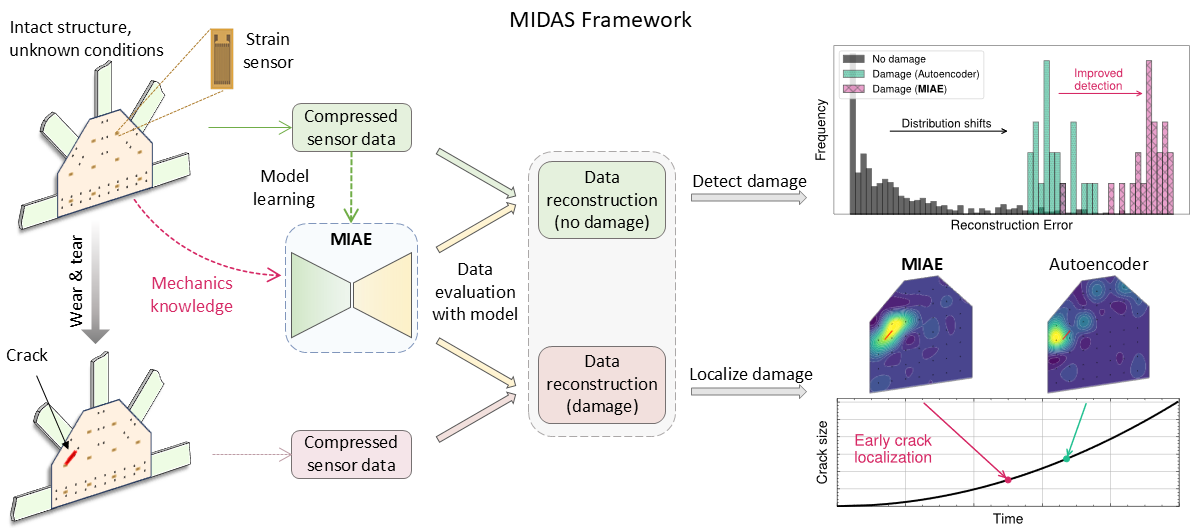
Key Findings
We demonstrate that MIDAS relies solely on reference data to establish an intact model reference and automatically detect unforeseen damage by tracking deviations from this reference, eliminating the need for training on labeled data or predefined damage conditions. By incorporating data compression techniques from inexpensive sensor measurements, MIDAS enables efficient data processing and near-real-time automated damage detection and localization.
A key component of MIDAS is the Mechanics-informed autoencoder, which leveraged the relationships between sensors positioned at various locations based on their mechanical strain responses. This enhances detection during early damage progression and enables earlier damage localization than traditional autoencoders by up to 35%. Our experimental evaluation shows consistently better performance from MIDAS than baseline methods, including autoencoders and support vector machines, across various statistical metrics. Additionally, MIDAS maintained high detection and localization accuracy even with limited sensors, noisy data, and temperature variations.
Looking Ahead
While MIDAS has demonstrated its potential on a variety of structures, its current applications are still in the early stages. The next phase involves expanding its deployment to more complex environments, such as entire buildings or multiple structures within a region. This expansion aims to establish MIDAS as a transformative solution for scalable and efficient infrastructure monitoring.
Achieving scalability requires integrating the physics of full-scale bridges and other structures into the MIDAS framework. Additionally, managing sensor data from diverse sources and handling diverse types of data introduces further complexity. By addressing these challenges, MIDAS can accommodate a wide range of infrastructure types and conditions, ensuring broad applicability. The vision extends to creating a unified monitoring system that can seamlessly manage and analyze large volumes of data from various structures, providing comprehensive insights into infrastructure health across extensive regions.
Overall, this work lays the foundation for realizing a broader vision of scalable, efficient infrastructure monitoring. By focusing on scalability and comprehensive applicability, MIDAS aims to transform how we assess and maintain the safety and resilience of our vital infrastructure systems.